Computational mechanics of
structures and materials
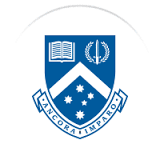

Hydraulic fracturing is a technique used to efficiently extract oil and gas trapped in rocks with a very low permeability. In a HF process, water is pumped under very high pressure into wellbores which breaks the rock and the cracks serve as pathways for oil and gas. A mathematical model of a HF process consists usually of the following components:
​
1. A poroelasticity (a la Biot) model for the rock
2. A fracture model to describe the initiation and propagation of the hydraulic fractures. Most often, linear elastic fracture mechanics (LEFM) or cohesive zone model (CZM) is adopted.
3. A fluid flow model for the fluid inside the fractures.
A parallel C++ code was written to model HF within the framework of the finite element method. In order to account for crack initiation and complex crack patterns, flow cohesive interface elements were developed. Using an object oriented programming paradigm, model (1)--for the porous medium and models (2,3)--for the fractures and the fluid inside are separated into two classes. Using the former class alone, one can model any poroelasticity problems. As a benchmark, the one-dimensional consolidation problem, also known as the Terzaghi problem, was analysed using the code. And the numerical solutions are in excellent agreement with the analytical ones.



Zero-thickness interface elements are placed along all element edges prior to the simulation to capture complex crack patterns without using remeshing. This can be done automatically using my code, ciGen. Each interface element has nodes along its mid-plane to model the fluid flow through it.
​
The code has been verified against known solutions using the well known KGD problem. The numerical wellbore pressure, crack mouth opening and the crack length agree well with the analytical solutions.

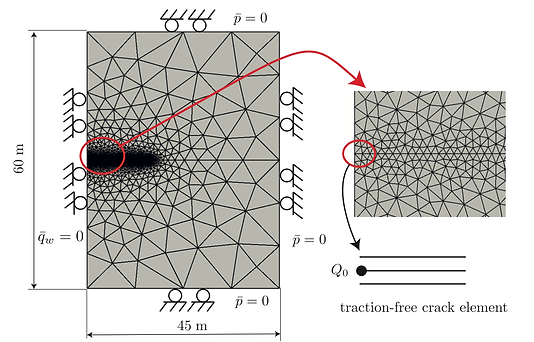

​
During this project it was discovered that phase-field approach to fracture offers a more flexible to perform hydraulic fracturing simulations. So some preliminary works have done on this exciting topic with Prof Jian-Ying Wu at South China University of Technology (Guangzhou). See Phase field modelling.
​
Some side projects on discrete element modeling of concrete and material point method based simulations of thin-walled tubes have been done via collaboration with Dr Sina Sinaie working with Prof Tuan Ngo at University of Melbourne. Some practical aspects of hydraulic fracturing were studied using Abaqus via a collaboration with Dr Behnam Sobhaniaragh.
​
In addition to numerical modeling, experimental work have also conducted through collaboration with the group of Prof Weiguo Liang at Taiyuan University of Technology (China).
​
A complete list of publications from this DECRA project can be found below.
References
-
V.P. Nguyen, H. Lian,T. Rabczuk and S. Bordas. Modelling hydraulic fractures in porous media using flow cohesive interface elements. Engineering Geology, 2017. link
-
V.P. Nguyen. Computational modeling of hydraulic fracture: state of the art, theory, implementation and benchmark tests. Monash University report. link
-
J. Y. Wu, V.P. Nguyen, C.T. Chi, D. Sutulas, S. Bordas, S. Sinaie. Phase-field modeling of fracture.
-
Y. Chen, W. Liang, H. Lian, J. Yang, and V. P. Nguyen. Experimental study on the effect of fracture geometric characteristics on the permeability in deformable rough-walled fractures. International Journal of Rock Mechanics and Mining Sciences, 2017 link
-
B. Sobhaniaragh, V.P. Nguyen, W.J. Mansur, F.C. Peters. Pore pressure and stress coupling in closely-spaced hydraulic fracturing designs on adjacent horizontal wellbores. European Journal of Mechanics-A/Solids, 2017 link
-
J. Yang, H. Lian, W. Liang, V. P. Nguyen and Y. Chen. Experimental investigation of the effects of supercritical carbon dioxide on fracture toughness of bituminous coals. International Journal of Rock Mechanics and Mining Sciences, 2018.
-
V. P. Nguyen and J. Y. Wu. Modeling dynamic fracture of solids with a phase-field regularized cohesive zone model. Computer Methods in Applied Mechanics and Engineering, 2018. link.
-
J. Y. Jian and V. P. Nguyen. A length scale insensitive phase-field damage model for brittle fracture. Journal of the Mechanics and Physics of Solids, 2018. link.
-
J. Y. Jian, J. F. Qiu, V. P. Nguyen, T. K. Mandal and L. J. Zhuang. Computational modeling of localized failure in solids: XFEM vs PF-CZM. Computer Methods in Applied Mechanics and Engineering, 2018. link.
-
S. Sinaie, T. D. Ngo, V.P. Nguyen and T. Rabczuk. Validation of the material point method for the simulation of thin-walled tubes under lateral comparison. Thin Walled Structures, 2018. link.
-
S. Sinaie, T. D. Ngo, and V.P. Nguyen. A discrete element model of concrete for cyclic loading. Computers & Structures, 2017. link.
-
S. Sinaie, V.P. Nguyen, C.T. Nguyen and S. Bordas. Programming the Material Point Method in Julia. Advances in Engineering Software,105: 17--29, 2017. link
-
V.P. Nguyen, C.T. Nguyen, T. Rabczuk and S. Natarajan. On a family of Convected Particle Domain Interpolations in the Material Point Method. Finite Elements in Analysis and Design 126:50-64, 2016. link
-
V.P. Nguyen, C.T. Nguyen, S. Bordas, A. Heidarpour. Modelling interfacial cracking with non-matching cohesive interface elements. Computational Mechanics, 58: 731–746, 2016.